Where Technology Meets Trust.
Khirat Khaleej Engineering Testing Company L.T.D
provide our clients with one of the most comprehensive inspection services available in the region.
From general and conventional inspection techniques to advanced inspection technologies, we are uniquely positioned to provide a robust inspection service.
With over 12 years of experience in providing reliable, high-quality inspection solutions across multiple industries, we have the tools and expertise needed to solve the toughest NDT inspection challenges to help the client get the most value out of NDT solutions, allowing him to achieve the efficiency, accuracy, and safety.

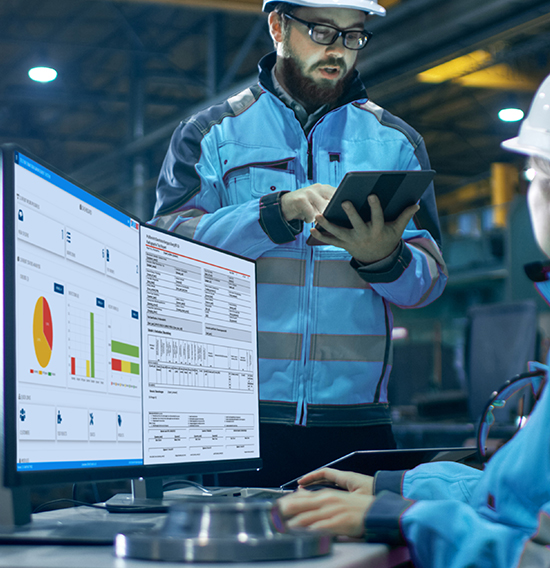
Providing Solutions for Inspecting Materials Without Causing Damage.
Many of modern construction projects and industrial facilities involve more complicated structures and severe working conditions than ever, therefore, any deficiencies or defects, no matter how small they seem to be, can lead to catastrophic accidents. So, engineering testing was a must, but, for economic considerations, it needs to be done on-site and with as limited damages as possible; here comes the need for non-destructive testing procedures.
As the name implies, non-destructive testing means conducting engineering examinations in order to detect any discontinuities within metallic or non-metallic materials, depending on the change of some physical properties, such as acoustic, magnetic and radiographic properties. Checking for welds defects is one of the most common applications of NDT techniques, since welds represent points of weakness and they often contain various types of flaws, for instance, cracks, porosity, splatter, undercut and so on.
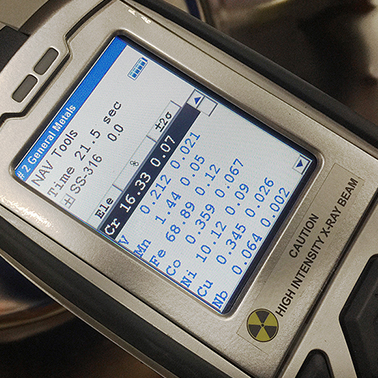
Industries We Serve
Oil Refineries and Oil Plants
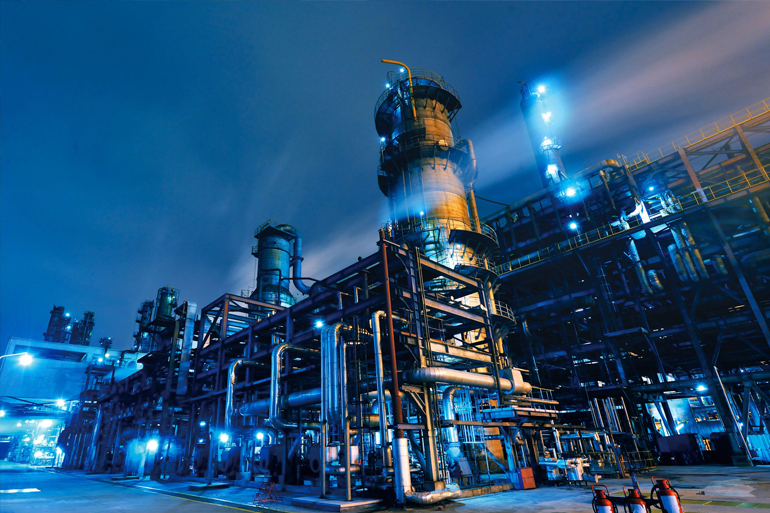
Oil Pipeline
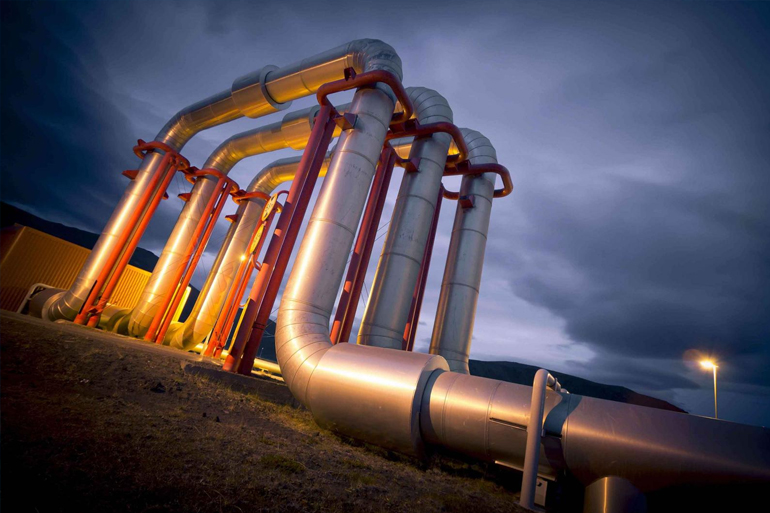
Natural Gas Pipeline
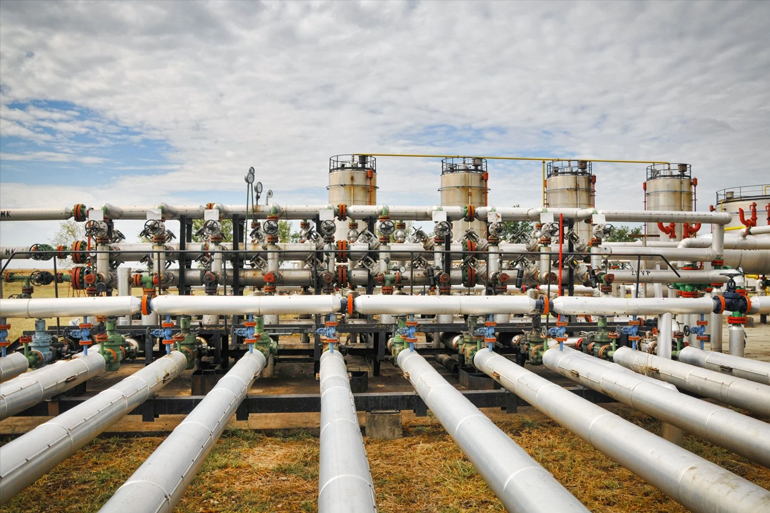
Natural Gas Plants
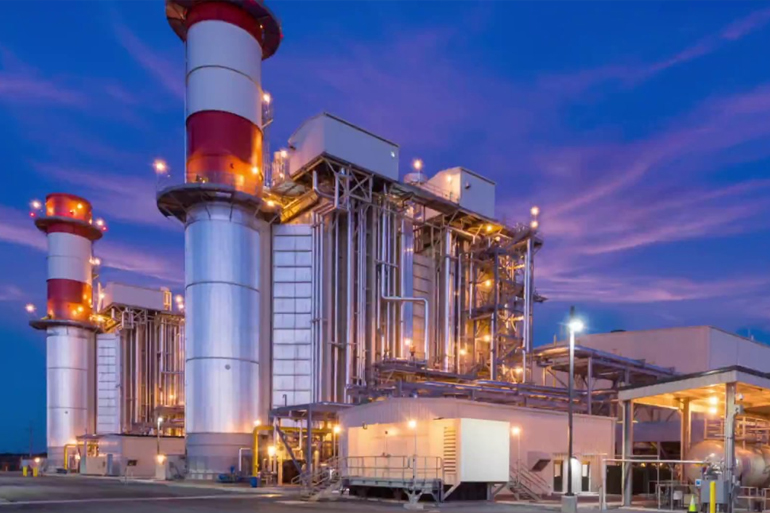
Water Plants
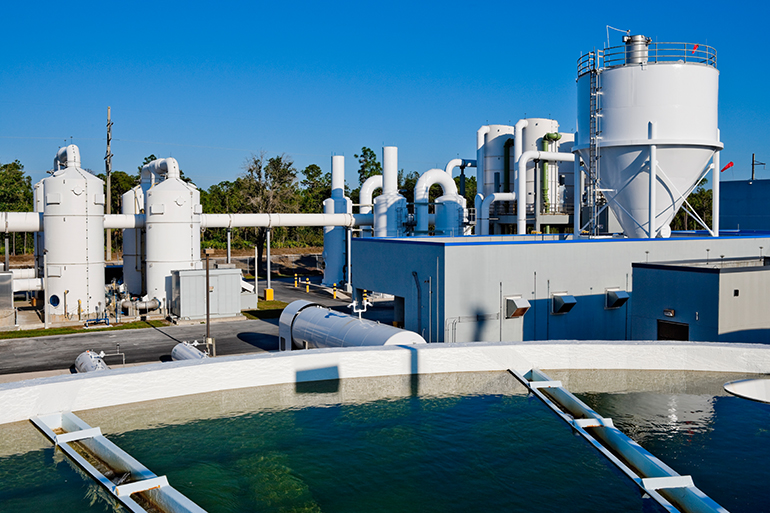
Compressor Stations
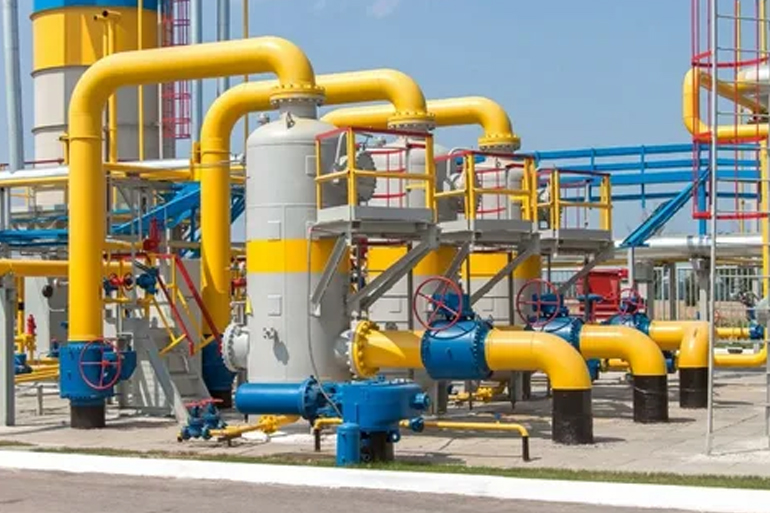
Oil, Gas and Water Tanks
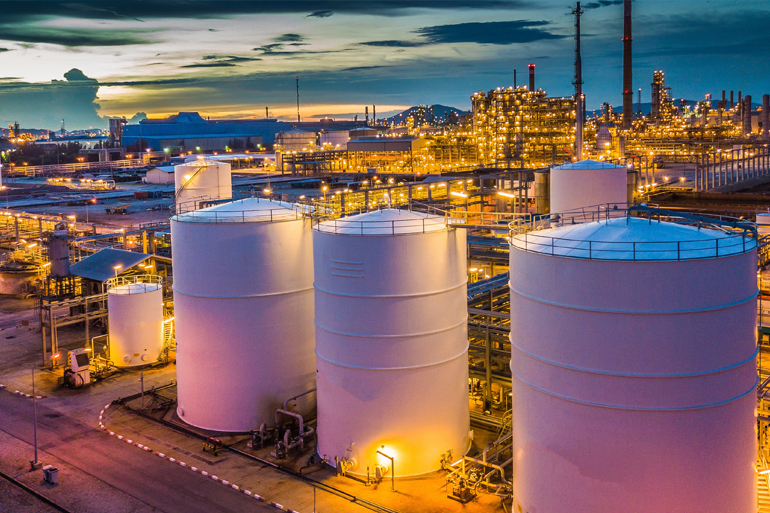
Petrochemical Industries
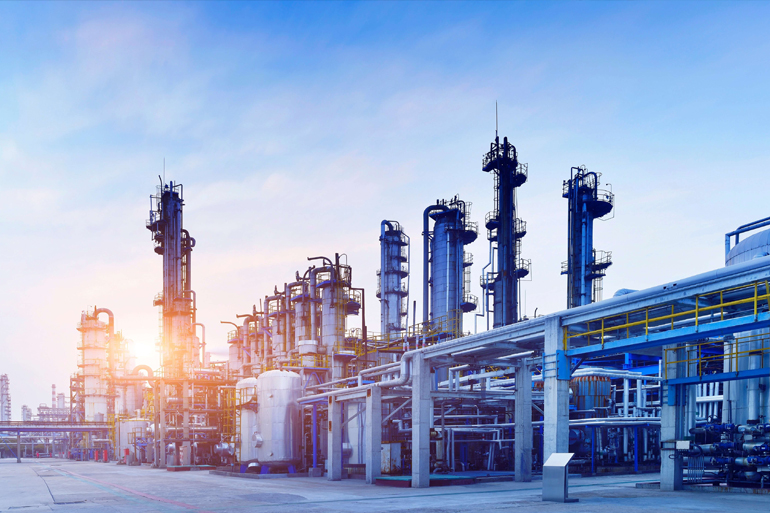
Power Generation Facilities
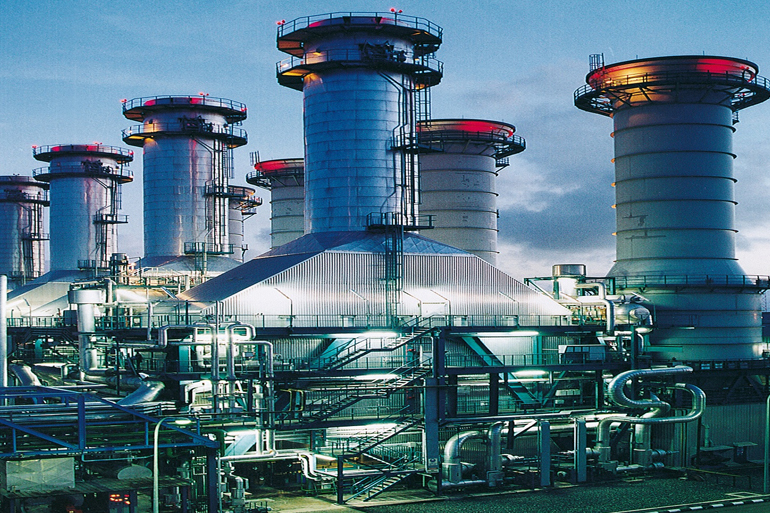
Steel Structure Factories
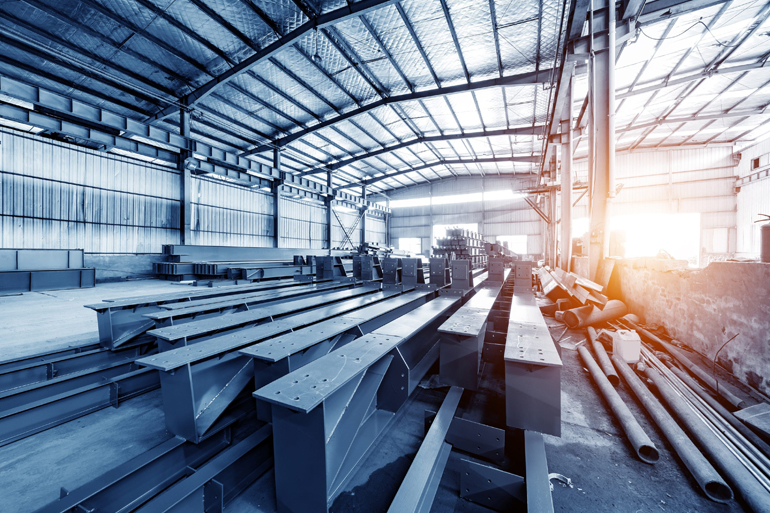