In-Service Inspection
In-service inspections are critical for maintaining the integrity and safety of various industrial assets, particularly in sectors such as oil and gas, petrochemicals, and power generation. Advanced Non-Destructive Testing (ANDT) plays a vital role in these inspections by providing detailed insights into the condition of materials without causing any damage. This approach allows for timely maintenance decisions that can prevent catastrophic failures and ensure compliance with regulatory standards.
Importance of In-Service Inspections
In-service inspections are essential for identifying potential issues before they escalate into significant problems. These inspections help organizations minimize downtime, optimize maintenance schedules, and enhance overall operational efficiency. By employing a NDT techniques, companies can detect flaws that traditional methods might miss, thus ensuring higher safety standards and reducing the risk of accidents.
Plant Integrity Inspection
Benefits of Plant Integrity Inspections
Increased Safety: Regular inspections help identify potential hazards before they lead to accidents.
Cost Savings: By detecting issues early, companies can avoid costly repairs and downtime associated with unexpected failures.
Regulatory Compliance: Inspections ensure adherence to industry regulations and standards, reducing legal liabilities.
Plant integrity inspection is a critical process in various industries, particularly in sectors such as oil and gas, power generation, and manufacturing. The goal of these inspections is to ensure that equipment and structures are safe, reliable, and compliant with regulatory standards. Non-Destructive Testing (NDT) plays a vital role in this process by allowing inspectors to evaluate the condition of materials and components without causing any damage.
Key Services Offered
The first step involves developing an inspection plan tailored to the specific needs of the client. This is often based on recognized methods such as Risk-Based Inspection (RBI), following standards like API 580/581.
After planning, the next phase is executing the inspection strategy using a variety of NDT techniques. These may include guided wave technology for inspecting pipes located in hard-to-reach areas such as road crossings or offshore installations.
Once inspections are completed, results must be validated through methods like Engineering Critical Assessment (ECA) and Fitness for Service (FFS) evaluations to ensure that any identified issues are addressed appropriately.
Pressure Vessel Inspection as per API 510 Advanced Digital Radiography (ART)
Importance of Advanced Digital Radiography (ART)
Advanced Digital Radiography (ART) is an innovative non-destructive testing (NDT) method that enhances traditional radiographic techniques. It utilizes digital imaging technology to produce high-quality images of the internal structures of pressure vessels without causing any damage.
This method is particularly beneficial in the context of API 510 inspections for several reasons:
ART provides superior image resolution compared to conventional radiography. This allows inspectors to detect smaller defects or irregularities within the material structure more effectively.
Unlike traditional methods that require film development, ART enables immediate viewing and analysis of images. Inspectors can quickly assess the condition of a pressure vessel during inspections, facilitating timely decision-making regarding repairs or further evaluations.
ART typically requires lower radiation doses than conventional radiographic methods. This not only enhances safety for personnel involved in inspections but also minimizes environmental impact.
The digital nature of ART allows for easy storage, retrieval, and sharing of inspection data among stakeholders. This capability supports better documentation practices and compliance with regulatory requirements.
ART can be applied to various materials and geometries commonly found in pressure vessels, making it a flexible option for inspectors working under API 510 guidelines.
Application in API 510 Inspections
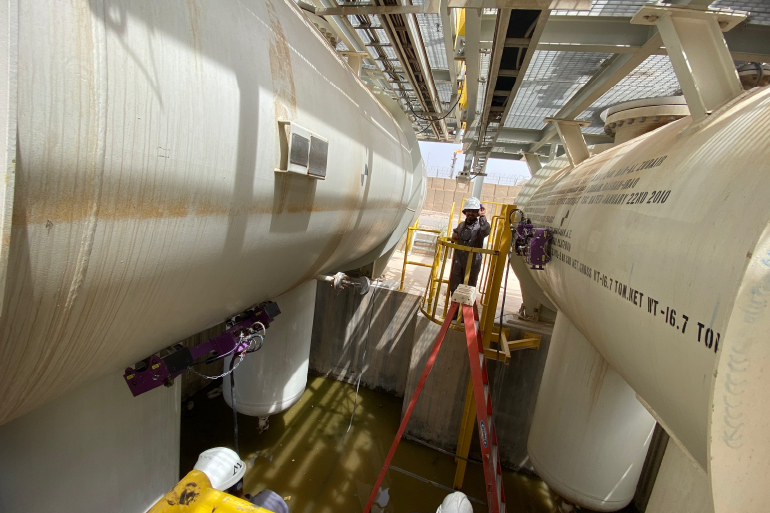
Storage Tank Inspection as per API 653
Purpose of API 653 Inspections
Inspection Frequency
- Tanks in service for less than ten years should undergo external inspections every five years.
- Tanks over ten years old require internal inspections every ten years.
- Newly constructed tanks must be inspected before being put into service
Inspection Process
The tank must be taken out of service, drained, cleaned, and made safe for entry.
Inspectors conduct a thorough visual examination of all accessible surfaces inside and outside the tank.
Techniques such as ultrasonic testing may be employed to detect hidden defects
Inspectors review historical data regarding previous repairs or modifications to assess current integrity.
A detailed report is generated post-inspection outlining findings, recommendations for repairs if necessary, and compliance status with API standards.
Types of Inspections
Conducted visually to assess the exterior condition of the tank. These should occur at least every five years.
Required for tanks that have been in service for ten years or more, these inspections must be performed every ten years. They involve entering the tank to check for internal corrosion, pitting, and other defects
Focus on assessing the tank’s floor for settlement or corrosion issues.
Evaluate the roof structure for signs of damage or deformation.
Examine the tank’s shell for any signs of bulging or deformation.
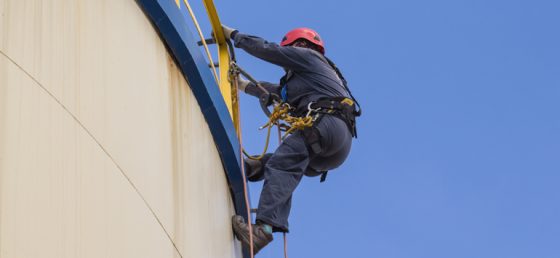
Piping Inspection as per API 570 Tank Floor Scanning Magnetic Flux Leakage
Overview of API 570
Importance of MFL in Piping Inspection
Magnetic Flux Leakage inspection utilizes a powerful magnet to magnetize steel components within pipelines or storage tanks. When there are defects such as corrosion or pitting, the magnetic field “leaks” from these areas. Sensors positioned between the poles of the magnet detect these leaks, allowing technicians to identify and evaluate defects without needing to remove or dismantle the piping system.
Advantages of Using MFL for Piping Inspection
MFL does not damage the material being inspected, allowing for ongoing use of assets.
The method allows for rapid scanning over large areas, providing quick results compared to traditional methods.
By identifying issues early, MFL can help prevent costly failures and extend asset life through targeted repairs rather than complete replacements.
Inspections can often be performed with access from only one side of a tank or pipe, which simplifies logistics and reduces downtime.
Process of MFL Inspection
The area around the pipeline or tank is prepared for inspection. This may involve cleaning surfaces to ensure accurate readings.
A strong magnetic field is applied using MFL tools designed specifically for this purpose. The equipment can be moved along the surface being inspected.
As the MFL tool scans the surface, it detects any distortions in the magnetic field caused by defects like corrosion or wall thinning.
Data collected from sensors are analyzed to determine the extent and severity of any identified issues. This information helps in making decisions regarding repairs or further inspections.
Results from MFL inspections are documented and can be used to establish baseline conditions for future assessments or compliance with regulatory standards such as API 653.
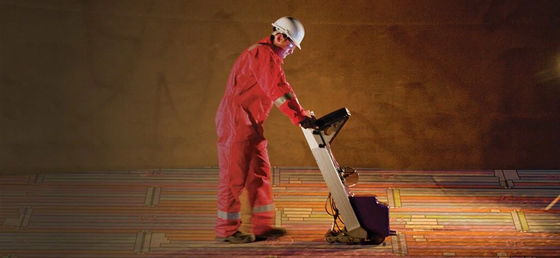
Welding Inspection Standards
CSWIP 3.1
The CSWIP 3.1 certification is a widely recognized qualification for welding inspectors developed by the Welding Institute (TWI). This standard focuses on the knowledge required to inspect welds effectively and includes topics such as:
- Welding Processes: Understanding various welding methods (e.g., MIG, TIG) and their applications.
- Weld Defects: Identifying common defects such as porosity, cracks, and incomplete fusion.
- Inspection Techniques: Utilizing visual inspection and non-destructive testing (NDT) methods like ultrasonic testing (UT) and radiographic testing (RT).
Inspectors certified under CSWIP 3.1 are expected to have a comprehensive understanding of these areas to ensure compliance with relevant codes.
AWS-CWI
The AWS Certified Welding Inspector (CWI) program is administered by the American Welding Society (AWS). It provides a framework for assessing the qualifications of welding inspectors in North America. Key components include:
- Fundamentals of Welding: Knowledge of welding metallurgy, processes, and equipment.
Code Compliance: Familiarity with applicable codes such as AWS D1.1 for structural steel welding.
Inspection Procedures: Skills in conducting inspections according to established protocols.
CWIs play a vital role in maintaining quality assurance in welding operations across various industries.
Applicable Codes
The ASME Boiler and Pressure Vessel Code, particularly Sections VIII and IX, outlines requirements for pressure vessels and piping systems:
- Section VIII covers the design and fabrication of pressure vessels.
- Section IX addresses welding qualifications necessary for personnel performing welds on these vessels.
These sections emphasize the importance of qualified welders who can produce sound welds that meet stringent safety standards.
The ASME B31 series includes several codes related to piping systems:
- B31.1 pertains to power piping systems.
- B31.3 focuses on process piping.
- B31.4 deals with liquid transportation pipelines.
Each code specifies requirements for materials, design, fabrication, installation, examination, and testing of piping systems to ensure safety and reliability.
The AWS D1.1 Structural Welding Code – Steel sets forth requirements for welding steel structures:
- It includes guidelines for pre-weld preparation, joint design, qualification of welders, and inspection criteria.
- The code emphasizes visual inspection as well as NDT methods to verify weld quality.
The API 1104 Standard for Welding Pipelines and Related Facilities provides guidelines specifically for pipeline construction:
- It covers procedures for qualifying welders and inspecting welded joints.
- The standard highlights the importance of maintaining consistent quality throughout the pipeline’s lifecycle.
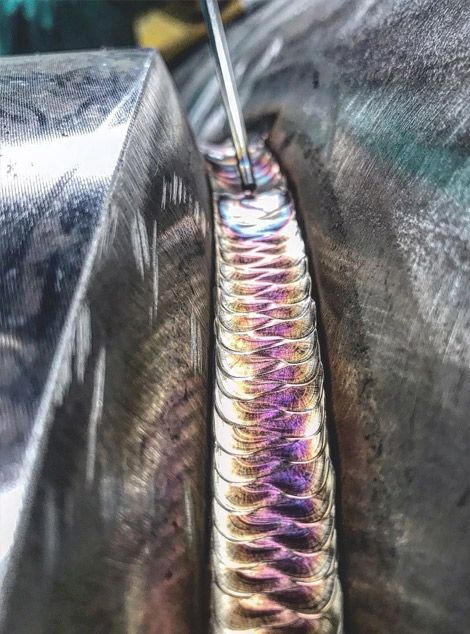