Destructive Testing
Destructive testing (DT) is a critical inspection method used to evaluate the performance and structural integrity of materials by subjecting them to extreme conditions that lead to permanent damage or failure. This approach is essential in various industries, including aerospace, automotive, construction, and manufacturing, as it provides valuable insights into material behavior under stress.
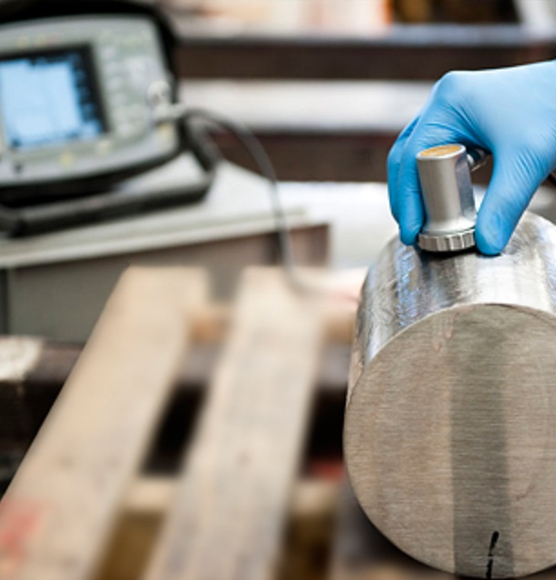
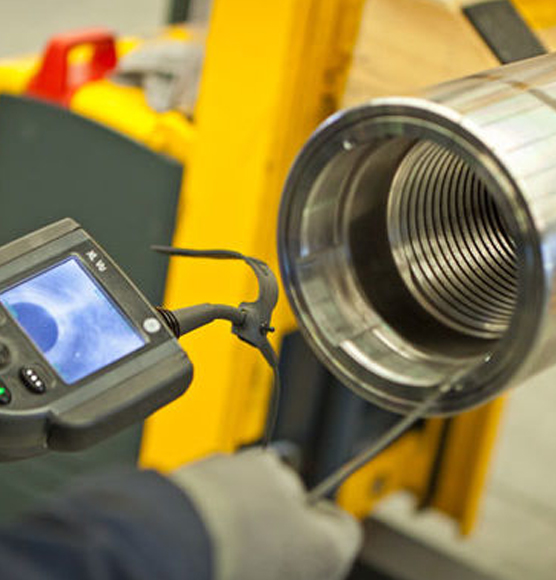
Key Characteristics of Destructive Testing
The primary characteristic of destructive testing is that it causes irreversible damage to the tested specimens. This means that once a sample has been tested, it cannot be reused or repaired.
The main goal of DT is to understand how materials behave under different stresses, loads, or environmental factors. By pushing materials to their breaking point, engineers can gather data on their limits and failure modes.
Destructive tests are typically conducted before mass production begins. This allows manufacturers to identify potential weaknesses in materials and ensure that products meet safety and quality standards.
Regular checks on lift/aerial equipment and other machinery to ensure operational safety.
Common Methods of Destructive Testing
This method measures how a material reacts when pulled until it breaks. It assesses tensile strength, elongation, and ductility.
Used to evaluate a material’s ability to absorb energy when subjected to sudden force or impact. Common examples include the Charpy and Izod tests.
Assesses a material’s resistance to corrosion under specific environmental conditions.
Measures a material’s resistance to deformation through indentation methods like Brinell or Rockwell tests.
Involves subjecting materials to repeated cyclic stresses to determine how long they can withstand fluctuating loads before failure occurs.
Determines the stress present within a material after manufacturing processes such as welding or machining.
Examines how materials fail or crack under load, helping identify potential failure modes and develop appropriate repair strategies.
Measures the slow deformation of materials under constant stress over time, particularly at high temperatures.
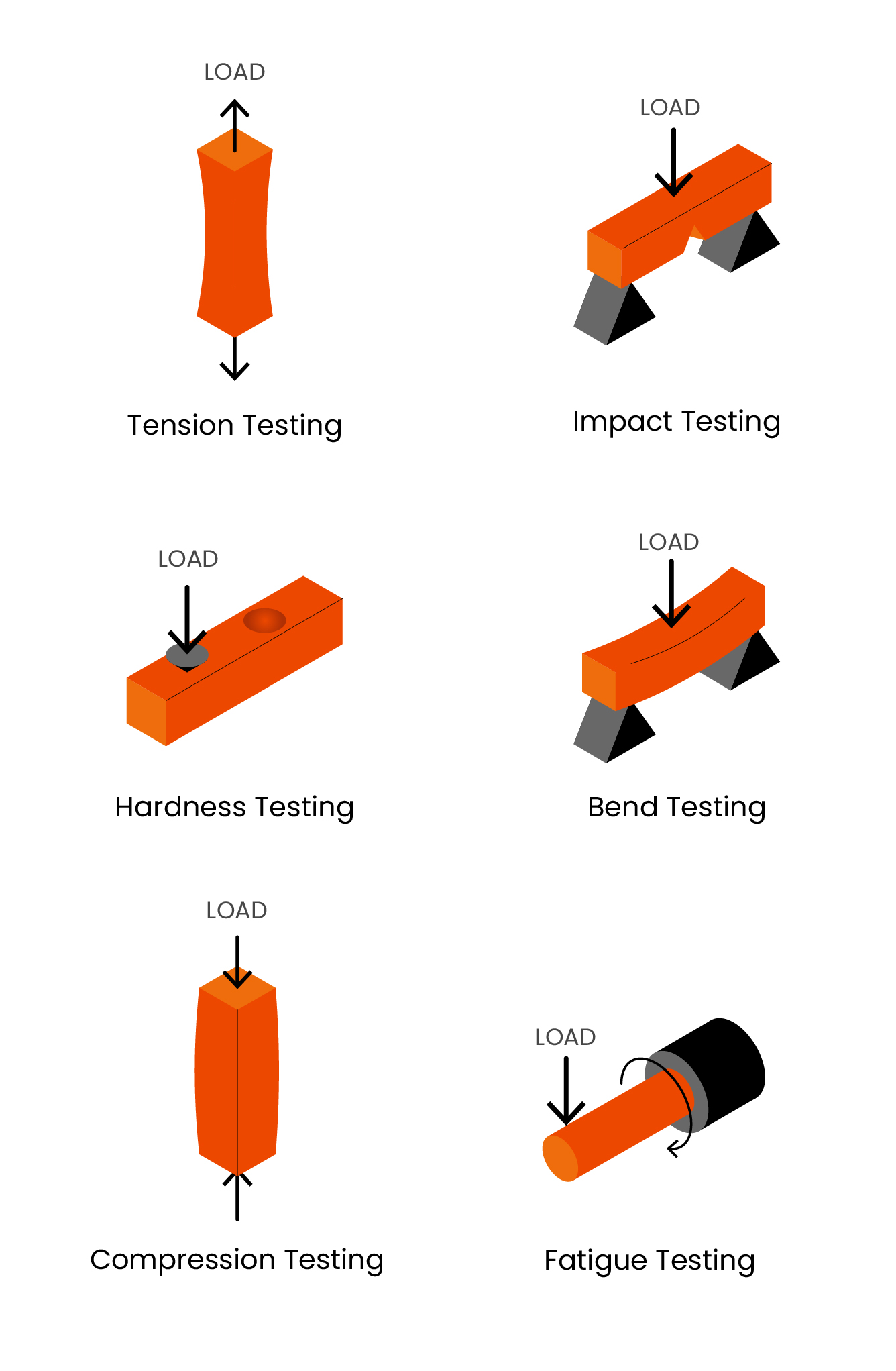
Applications of Destructive Testing
Aerospace Industry: Ensures components can withstand extreme conditions through fatigue and tensile testing.
Automotive Sector: Evaluates crashworthiness and durability using impact and tensile tests.
Construction Industry: Assesses compressive strength in concrete and steel for structural safety.
Manufacturing Sector: Guarantees product quality through various destructive tests like bend testing and fracture analysis.