Other Services
A wide range of techniques and services that are essential for ensuring the integrity and safety of materials and structures without causing any damage.
Our services play a crucial role in various sectors by facilitating inspections.
Painting and Coating Inspection
Types of Coating Inspections
There are various types of inspections conducted during the painting and coating process:
This test measures the thickness of the cured coating to ensure it meets specifications. DFT is crucial because insufficient thickness can compromise protection against corrosion.
Conducted immediately after application, this measurement assesses the thickness of the wet coating to predict final dry film thickness and ensure adequate coverage.
This non-destructive test identifies discontinuities in coatings such as pinholes or voids that could allow corrosion to occur beneath the surface.
This ensures that the surface texture is appropriate for optimal adhesion of the coating.
Importance of Coating Inspection
Coating inspections serve several essential purposes:
- Quality Assurance: Inspections ensure that the coatings meet specified standards and are applied according to industry regulations. This includes verifying surface preparation, application methods, and environmental conditions during application.
- Corrosion Prevention: Corrosion is a significant threat to infrastructure such as bridges, pipelines, and storage tanks. Effective coating inspection helps identify potential issues before they lead to severe damage or failure.
- Cost Efficiency: By identifying defects early through thorough inspections, companies can avoid expensive repairs or replacements later on. Preventative maintenance through regular inspections can save organizations substantial amounts of money over time
Welder/Welding Procedure Qualifications
Procedure Qualification Record (PQR)
The Procedure Qualification Record (PQR) is a document that certifies that a particular welding procedure has been tested and meets required codes and standards. The PQR is developed by performing tests on welded samples created according to the WPS. These tests may include visual inspections, mechanical testing (like tensile strength tests), or non-destructive testing methods.
The PQR contains crucial information such as:
- Identification of the WPS used.
- Results from various tests performed on the test coupon.
- Any limitations or restrictions associated with the welding procedure.
This record provides evidence that the specified welding procedure can produce welds meeting quality requirements
Welding Procedure Specification (WPS)
The Welding Procedure Specification (WPS) is a detailed document that outlines how a specific welding job should be performed. It includes essential variables such as:
- Type of welding process (e.g., Shielded Metal Arc Welding, Gas Tungsten Arc Welding).
- Base materials and filler metals.
- Joint design.
- Preheat and post-weld heat treatment requirements.
- Electrical characteristics like amperage and voltage.
- Position of the weld.
The WPS serves as a guide for welders, supervisors, inspectors, and quality control personnel to ensure consistency and compliance with applicable codes and standards.
Welder Performance Qualification (WPQ)
The Welder Performance Qualification (WPQ) documents an individual welder’s ability to produce acceptable welds according to a specific WPS. This qualification is typically achieved through practical assessments where the welder performs actual welding tasks under controlled conditions.
Key aspects of WPQ include:
- Verification that the welder can follow the WPS accurately.
- Documentation of essential variables during testing.
- Results from tests conducted on welds made by the welder.
A successful WPQ indicates that a welder possesses the necessary skills to perform high-quality work in accordance with industry standards
Post Weld Heat Treatment (PWHT)
Importance of PWHT
Welding introduces significant thermal gradients and residual stresses into materials. These stresses can lead to various problems such as distortion, cracking, and reduced mechanical performance of the welded joint. The primary benefits of PWHT include:
- Relaxation of Residual Stresses: The heating process allows the material to expand and subsequently contract uniformly, which helps in reducing the internal stresses that could lead to cracking or distortion.
- Improved Mechanical Properties: PWHT enhances toughness and ductility while reducing hardness, making the welded joint more resilient under dynamic loading conditions. This is particularly important for applications in high-stress environments like pressure vessels and piping systems.
- Hydrogen Removal: During welding, hydrogen can be absorbed into the metal, leading to hydrogen-induced cracking (HIC). PWHT helps diffuse this hydrogen out of the weld area.
- Prevention of Stress Corrosion Cracking: By reducing residual stress levels, PWHT also lowers the risk of stress corrosion cracking, especially in corrosive environments.
Techniques Used in PWHT
Involves heating the welded joint to a specific temperature for a set duration followed by slow cooling. This method is commonly used for low-carbon steels
This technique heats the material to a higher temperature than annealing followed by rapid cooling. It improves homogeneity and reduces hardness
Typically applied to high-strength materials where rapid cooling is followed by reheating at lower temperatures to achieve desired mechanical properties.
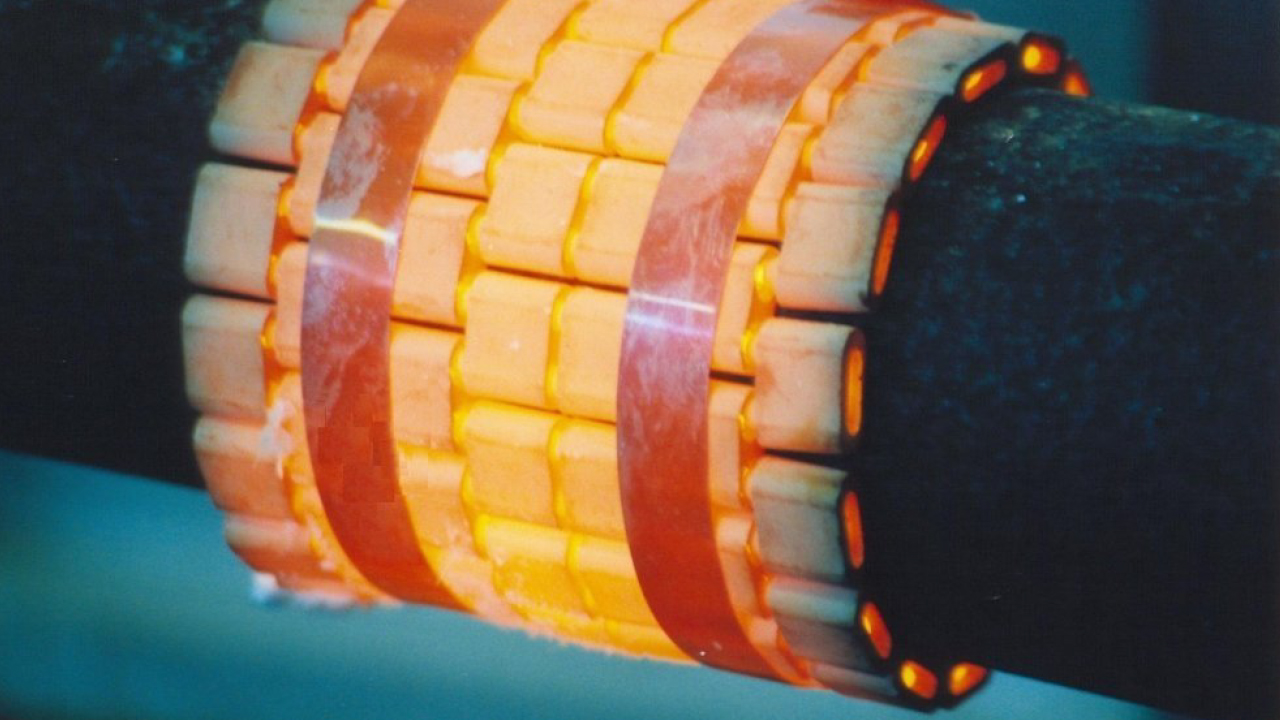
Risks of Not Performing PWHT
Neglecting PWHT can result in several detrimental effects:
- Increased susceptibility to brittle fracture due to high residual stresses.
- Higher likelihood of weld failures under load due to reduced tensile strength.
- Potential for stress corrosion cracking when combined with corrosive environments
Vacuum Box Leak Inspection
Vacuum box leak inspection is a method used primarily to identify leaks in welds, tanks, and other sealed components. This technique is particularly useful for areas that cannot be pressurized directly, allowing for effective detection of leaks without damaging the tested materials.
Advantages of Vacuum Box Testing
The vacuum box method offers several advantages:
- It can detect very small leaks effectively.
- Provides immediate visual confirmation of leak locations through bubble formation.
- Allows for rapid inspection over large areas without significant disruption to operations.
- Requires access only from one side of the component being tested
Applications of Vacuum Box Testing
Aerospace and Defense: Guarantees reliability in critical components used under high-stakes conditions
How the Vacuum Box Method Works
A bubble-forming solution is applied to the area being tested. This solution must be specifically designed for leak detection and should not include household soaps or detergents, which are not suitable for this purpose
A vacuum box, which has a transparent viewing window and is equipped with a gasket to create an airtight seal, is placed over the area where the leak is suspected. The box must be capable of maintaining a pressure differential of at least 8 psi
The air inside the vacuum box is evacuated to create a negative pressure relative to the outside atmosphere. This differential pressure causes any gas leaking through defects in the material (such as cracks or pores) to pass through the bubble solution
As gas escapes from leaks in the material, it will disrupt the surface tension of the bubble-forming solution, resulting in visible bubbles forming at the leak sites. The presence and size of these bubbles can indicate both the location and severity of any leaks present
After conducting the test, technicians analyze the results to determine if there are any leaks present and provide detailed reports on their findings.
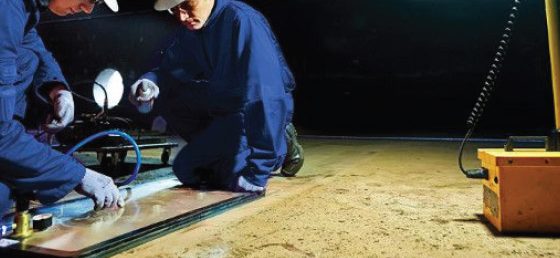
Pressure Testing (Hydrostatic & Pneumatic)
Pressure testing is a critical non-destructive method used to verify the integrity, strength, and leak-tightness of equipment such as pipelines, pressure vessels, plumbing systems, gas cylinders, boilers, and fuel tanks. It ensures that these components can safely withstand their rated pressures under operational conditions. The two primary methods of pressure testing are Hydrostatic Testing and Pneumatic Testing, each with its own applications, advantages, and risks.
Both methods are governed by industry standards such as the ASME B31 Pressure Piping Code, which includes specific guidelines for different types of piping systems like power piping (ASME B31.1), process piping (ASME B31.3), and refrigeration piping (ASME B31.5). These codes ensure consistency in procedures and safety across industries.
Hydrostatic Testing
Hydrostatic testing involves filling the system or component with a liquid—typically water—and pressurizing it to a level higher than its normal operating pressure. This test is used to check for leaks and assess the structural integrity of the system.
Procedure
- Filling the System: The system is filled with water or another non-toxic liquid.
- Pressurization: The pressure is gradually increased to a predetermined level (usually 1.5 times the design pressure for most systems).
- Leak Detection: The system is held at this pressure for at least 10 minutes while all joints and connections are inspected for leaks.
- Depressurization: After completing the inspection, the pressure is slowly released.
Advantages
- Safety: Water is incompressible, meaning it stores very little energy under pressure compared to gases. This makes hydrostatic testing safer than pneumatic testing.
- Accurate Leak Detection: Because water does not compress significantly under pressure, even small leaks can be detected easily.
- Realistic Simulation: For pipelines carrying liquids, hydrostatic tests closely mimic real-world operating conditions.
- Environmental Friendliness: Water is non-hazardous and eco-friendly compared to gases used in pneumatic tests.
Pneumatic Testing
Pneumatic testing uses compressed gas—commonly air or nitrogen—to pressurize a system for integrity checks. It is often employed when using liquids like water would be impractical or undesirable.
Procedure
- Preliminary Check: A low-pressure preliminary test (e.g., 170 kPa or 25 psi) may be conducted to locate major leaks before full pressurization.
- Gradual Pressurization: The system’s pressure is gradually increased in steps until reaching the required test level (typically 1.2–1.5 times the design pressure).
- Leak Inspection: Joints and connections are inspected using methods like soap bubble solutions.
- Depressurization: After inspection, the gas is carefully vented from the system.
Advantages
- No Moisture Introduction: Ideal for systems where moisture could cause damage or contamination.
- Faster Process: Pressurization and depressurization occur more quickly than in hydrostatic tests.
- Temperature Stability: Gas-based tests are less affected by temperature changes compared to liquid-based tests.
X-Ray Digitalized Film
Importance of Digitizing X-Ray Films
- Firstly, it allows for the preservation of the original film’s image quality while eliminating the aging of films.
- Secondly, it enables the efficient management of image data and facilitates the comparison of past and present inspections.
Film Preparation and Quality
The quality of the X-ray film used in NDT is crucial for obtaining accurate inspection results. Manufacturers like Fujifilm produce high-quality industrial X-ray films designed for consistent performance and compatibility with various NDT chemistries and processing conditions.
Applications and Industries
X-Ray digitalized film NDT is applied in various industries, including aerospace, oil and gas, power generation, and manufacturing. It is used for inspecting welds, detecting corrosion and erosion in pipes, examining turbine blades, and other critical components.
Technology Used in Film Digitization
The technology used for digitizing X-ray films includes film digitizers that convert analog films into high-quality digital images. These digitizers are designed to handle a wide range of film types and sizes, ensuring that the digital images accurately represent the original films.
Companies like CAD/CAM Services provide film digitizing services for NDT, helping organizations transition from analog to digital imaging.
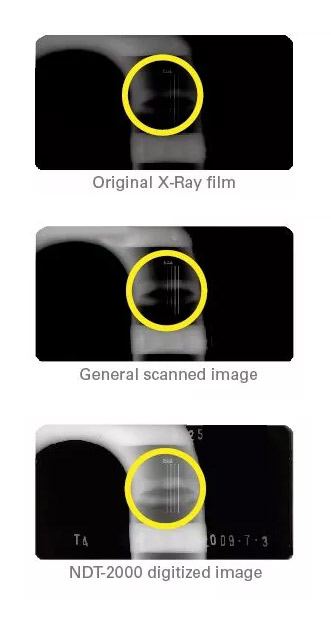
Benefits of Digital Radiography in NDT
Digital radiography has become increasingly popular in NDT due to its numerous benefits.
It enhances inspection efficiency, productivity, and profit margins by providing immediate digital images that can be analyzed and shared easily.
The use of digital radiography also supports continuous product improvement by allowing for the easy comparison of current and past inspections.
The key benefits of NDT film digitizing include:
- Eliminates aging of films, retaining image quality
- Physical archive storage to the computer or Diconde Cloud
- Associated documents such as UT, MPI, and associated reports can also be archived
- Radiographs can be electronically reported and archived
- With Diconde Cloud, information is available to authorized users 24/7 from any Internet browser
- Eliminates storage costs of film